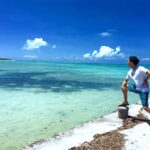
こんにちは!データサイエンティストの青木和也(https://twitter.com/kaizen_oni)です!
今回の記事では、「カンバン方式」「ジャスト・イン・タイム生産」「5WHY」の原典とも言える1冊「トヨタ生産方式 –脱規模の経営をめざして–」を読んで得た学びについてみなさんにご紹介させていただきたいと思います。
本書は高度経済成長の「多産多売」の時代から、だんだんと日本停滞期に差し掛かった頃にスポットライトを浴びたトヨタの生産方式「ジャスト・イン・タイム生産」をはじめとした、当時画期的とされた生産現場のあり方について書かれた書籍になります。
いわば、現代のリーン開発の先駆けとも言える書籍です。
本記事を通じて、リーン開発の原点が与えてくれる示唆のエッセンスを掴んでいただけると幸いです。
本書の概要
本書はトヨタ自動車工場における「ジャスト・イン・タイム生産」(=必要な時に必要な数だけ生産する方式)や「カンバン方式」(=カンバンという製品に関する情報が書かれたメモが工場内を行き来することによって、前工程の部品の準備などがスムーズに行われる方式)の導入初期において尽力したトヨタ自動車工場の工場長である大野さんが、トヨタ生産方式について述べた1冊です。
大量生産によるコストの減少が基本的な製造業の戦略であった時代に、あえて少量を必要な時に作るという事例のないことに取り組まれていた、というのが話の大枠になります。
つまり、工場という場でイノベーションを起こしていた方のまさに自伝ともいうべき1冊なのです。
本書の章立ては以下のようになっています。
- ニーズからの出発
- トヨタ生産方式の展開
- トヨタ生産方式の系譜
- フォード・システムの真意
- 低成長時代を生き抜く
後半はトヨタの歴史書的な内容になっています。
トヨタ生産方式の真髄が詰まっているのは序盤で、かなり濃厚な内容となっています。
本書から得た学び
私が本書から得た学びは以下の3点です。
- 正常時は人がいらず、異常時に人が必要になるような仕組みを作れ
- 質ではなく量を追い求めるのは脳死
- 「省力化」ではなく「少人化」
順を追って解説していきます。
正常時は人がいらず、異常時に人が必要になるような仕組みを作れ
この自動機にニンベンをつけることは、管理という意味も大きく変えるのである。すなわち人は正常に機械が動いているときにはいらずに、異常でストップしたときに初めてそこへ行けばよいからである。だから一人で何台もの機械が持てるようになり、工数低減が進み、生産効率は飛躍的に向上する
大野耐一『トヨタ生産方式 –脱規模の経営をめざして–』(ダイヤモンド社/2020) P15
本書ではたびたび「自働化」という言葉が登場する。
この言葉の意味としては上記引用文で述べられているように、自動で動くことに加えて【自動で止まる機能】が付いた機械のことを指す。
この自働化は元々、工場において人の配置が必要なのは機械に想定外のエラーが発生した際に対処をする、もしくは機械を止めるためだとされていた。
しかし、そうであるならば機械自身が勝手に止まってくれる仕組みを作れば、配置すべき人員も減らせるはずである、という論理を展開している。
また、本書では一貫して「ムダの排除」について言及している。
機械が異常である時に発生してしまうムダは「不良品の生産」というムダだ。
不良品を生産してしまうような状況で、機械がそれを検知し止まってくれれば当然のことながら不良品というムダなものは減少するはず、という論理だ。
さて、この「自働化」について現代の我々に与えてくれる示唆は何か。
それは、「RPA」などの自動化を行うときに、異常が発生したら通知するような仕組みをフローの中に組み込む必要があるということだ。
つまり、「通知がない限りは放っておいてOK」という状態を作ることが効率化アップのミソということである。
逆にこの通知機能を作らなければ、「毎日正常にRPAが動いているかをチェックする仕事」を持つ人間が発生してしまうことになり、ちりつもで大きな工数をムダにしてしまう。
特に現代においては生成AIの登場によって人々の生産性は指数関数的に増加しているので、人間が創造的なことに使う時間を減少されるような保守業務というのは少なければ少ないほどよい。
「自動化された何かについて人が関わる手間を最小限にするためにはどうすればいいか」を考えることがデジタライゼーション・DXを考える人間には必要となってくる。
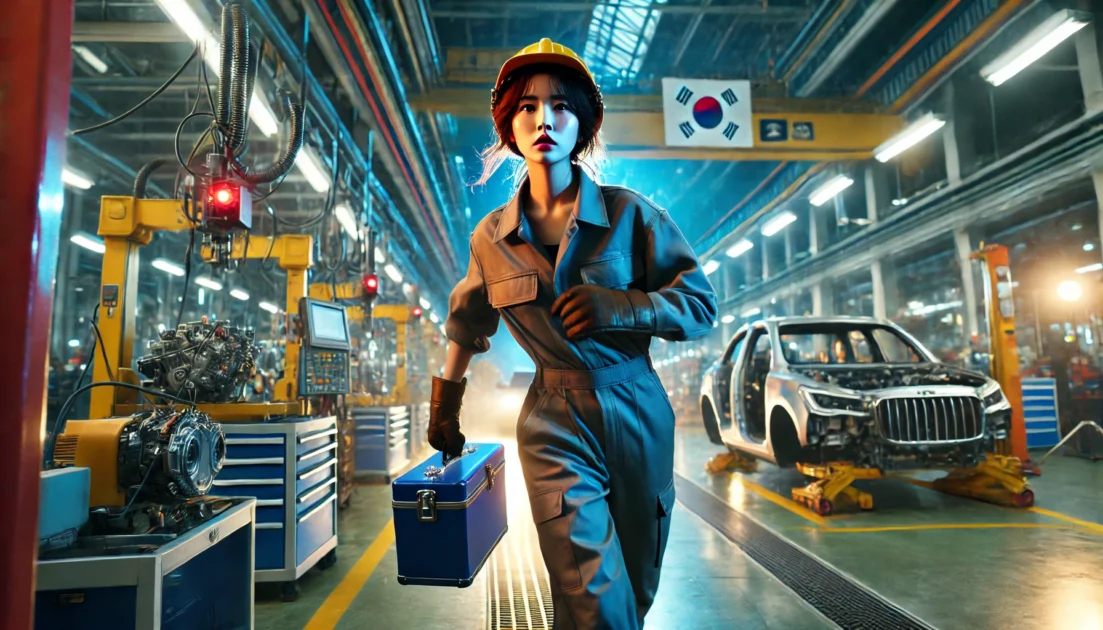
質ではなく量を追い求めるのは脳死
他人が量を増やせば気が気ではなくなり、自分も設備をふやして売り上げを伸ばす。真の能率を問うことなしに、機械をふやし人をふやしてきただけに、売上は伸びても、利益率はいっこうに伸びない。それで満足していたとしたら、これはもはや経営以前の話である。
大野耐一『トヨタ生産方式 –脱規模の経営をめざして–』(ダイヤモンド社/2020) P118
例えば、SESのような抱えている従業員数がそのまま売上に直結するような業態では、売り上げを向上させるのに採用人数を増やそうと考えるのはストレートな解決策ではある。
反面、人を雇えば雇うほど増加するコスト(教育に関わる投資、経理・総務の作業量、営業活動等々)がある。
一方で、現在抱えている従業員のSES単価を上げるような試みは、一時的なコストはかかるものの、定常的に採用活動をして人を増やし続けるよりかは利益率の高い行為であると考えられる。
売り上げという分かりやすい指標を追いかけて何かを増やす(例えば人員、例えば生産数、例えばサービス数)ことも時には必要だが、考えるべきは一つ一つまたは一人一人をいかに効率的に動かすか、という全体感を持った視点である、ということを本書では述べられている。
特に、現代においてはパラレルワーク(副業)をしている人も散見されるが、基本的に人は24時間を拡張する、という戦略は取れない。
そうすると、必然的に単位時間あたりの生産性を上げるか、何かムダなことをやめる以外に本業と副業を両立される手段はないのだ。
そういう意味では、本書の中の以下引用文も非常に示唆深い。
10年以上も前のこと、ある会社の焼き入れ工場を見に行った。 当時は月産7万台ぐらいだったが、「うちはもう、トヨタさんが10万台作っても迷惑をかけないだけの人員と設備を備えている」と言う。
「では、1ヶ月のうち10日間は工場を休むのか」と聞いたら、「いや、そんなバカなことはしない」と答える。
前工程の機械加工のところへ行ってみると、女子作業者が目の色を変えて働いている。炉が遊ぶともったいないから、ということで最大限に働いている。
大野耐一『トヨタ生産方式 –脱規模の経営をめざして–』(ダイヤモンド社/2020) P119
ムダなことはやめる勇気を持つことの重要性を示唆してくれる一節だ。
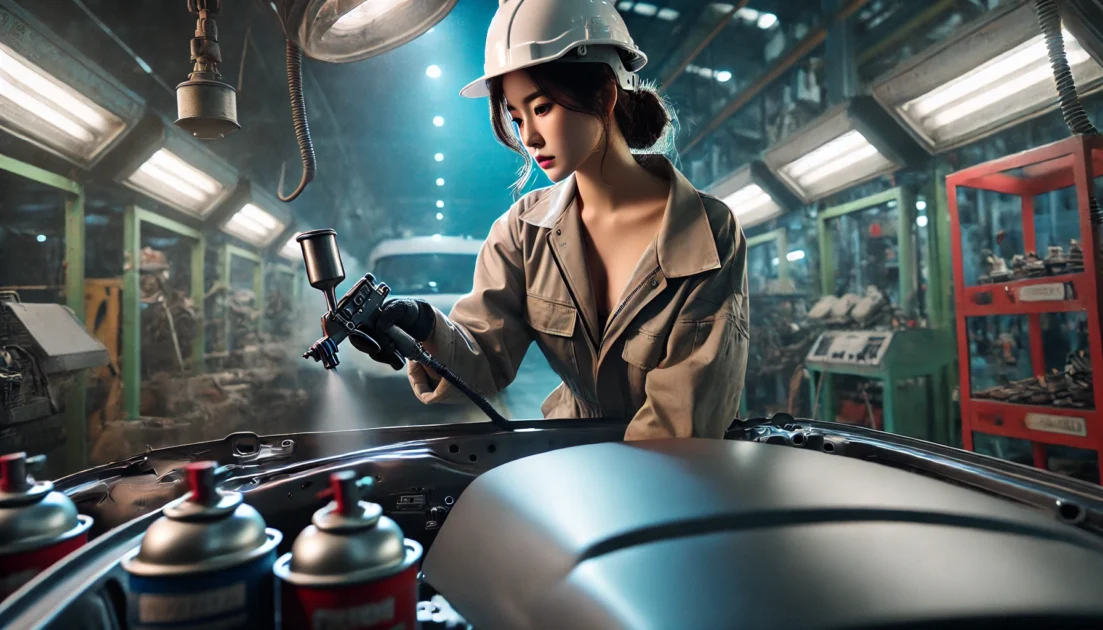
「省力化」ではなく「少人化」
大きな生産量を、いかに少ない人数でやるか。これを工数で考えると間違う。人間の数で考える。というのは0.9人分の工数を減らしても、「省人化」にはならないからである。
大野耐一『トヨタ生産方式 –脱規模の経営をめざして–』(ダイヤモンド社/2020) P119
つまりは、全体工数の削減が重要なのではなく、1人あたり生産性の向上が重要である、ということである。
トヨタ自動車工場では、「省人化」という言葉よりも「少人化」という言葉を使っていたようだが、その意味は「人員を省くのが目的ではなく、少ない人員で生産量をキープできるようにしよう」という考え方が根底にあるようだ。
現代に置き換えて考えると、中途半端な自動化では多少の改善にはつながっても、抜本的な改善にはつながらないと考えられる。
そうした場合には、どれだけのインパクトがあることを自動化するのか、極力人の作業が介在しないためにはどのような仕組みを作ればいいのか、とマクロな視点から業務改善・改革の価値というのを捉える必要がある。
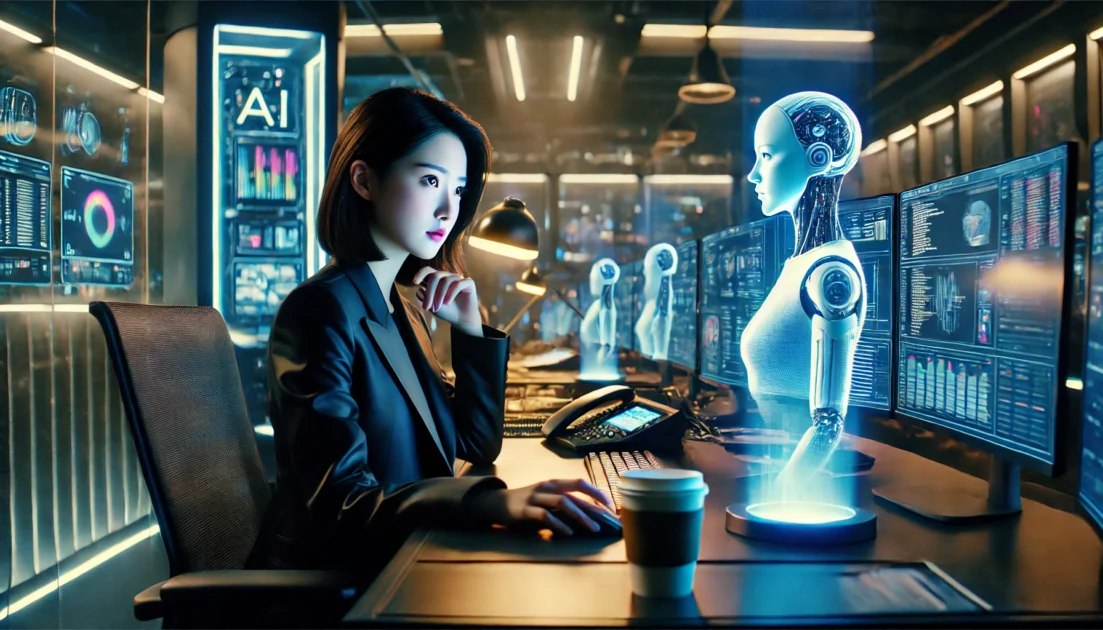
まとめ
今回の記事では、「カンバン方式」「ジャスト・イン・タイム生産」「5WHY」の原典とも言える1冊「トヨタ生産方式 –脱規模の経営をめざして–」を読んで得た学びについてみなさんにご紹介させていただきました。
自身が企業のDX推進的な業務を行なっているからか、自動化に関連したTipsが多く紹介してしまったような気がしますが、本書にはそれ以外にも「原因を深く掘り下げる重要性」「発想を逆転させてみることの重要性」「生産性を上げるためであれば、ムダは限りなく排除し、減価償却という短期的な視点にとらわれない姿勢」など多くのことを学ぶことができます。
トヨタ式の効率抜本改善法に興味のある方はぜひ本書をお手に取ってみてください!
コメント